The fiber-type OPELASER Lite was released in 2002, with the aim being that as a fiber-type laser and as part of the OPELASER series it would have vaporizing and cutting qualities, but its sales were also boosted beyond our expectations by its compact design. At the same time, the manipulator that has become an integral part of the Yoshida tradition was evolving as the 03Series from the first release in 1994 of the 03S, then on to the 03SII and then to the current 03SIISP model. But even though the company's compact fiber-type Lite model proved popular, the large size was still a problem, for example making it too heavy for hygienists to move easily around the surgery or clinic. Sales representatives gathered a lot of feedback on how the 03SIISP could be improved.
The OPELASER Lite had been designed to highlight its vaporization and incision qualities, but the 03SIISP had a beam delivered by the manipulator which had clarity and sharpness, enabling highly impressive cutting and vaporization performance. The quality of the laser beam and the ease of use of the model made us confident that doctors would want to use the product.
"What's the difference in the laser delivery between the Lite (fiber-type) and the 03SIIP (manipulator-type)?"
The OPELASER Lite, being a fiber type, appears easy to operate. Actual performance does in fact show that it's easy to use for low-intensity work, but for high-intensity work the laser point diameter is too large and there is not much concentration depth, making the manipulator more appropriate.
The 03SIISP manipulator-type, on the other hand, appears to be difficult to operate. However, the design is focused on the movement required for treatment procedures, so once the position of the apparatus body is fixed, the laser point size, appropriate concentration depth and responsiveness make it easy to use even for beginners. The only hurdle to overcome is the preconception that it will be cumbersome to use...

Laser quality brings a new lease of life to the manipulator.
While the OPELASER Lite was still under development in 2001, the plan was devised to have a two-track approach, with the fiber-types in the Lite range and the manipulator-type in the PRO range.
To justify the 'PRO' tag would require the installation of a high quality laser to add to the maneuverability already enjoyed by manipulator users.
We set three conditions that the manipulator would have to meet to truly deserve its status as No.1 choice:
1.It had to be easy to use
2.It had to be compact and stylish
3.The laser had to be high quality

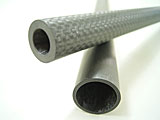
Previous models had used aluminum pipes, but the pipes' lack of rigidity meant that not enough precision could be achieved to make full use of the end tip's qualities. We looked for harder material, and after some research decided that, because with metals the weight increases in relation to the strength of the material, we would opt for non-metal materials. Despite the higher costs involved, we decided to use carbon.
¦Carbon is a strong and light material with a relative density of 1.7
i(relative density for aluminum and iron are 2.7 and 7.9 respectively).
Carbon fiberfs tensile strength is also twice that of iron.
When carbon fibers are combined with resin to form a hard compound, the composition of the fibers can have a major impact on the material's characteristics.
For example, by increasing the amount of the material wrapped in a circumferential direction the pipe's radial strength can increased, while if more material is laid lengthways then the pipe's rigidity can be increased. The common cross-lined pattern indicates equal application of 50% both vertically and horizontally.
For our design, we decided to remove a lot of the vertical material to increase the rigidity. The resulting pipe has the same resistance to bending as iron, but is as light as aluminum.
Using carbon material means that even if the diameter is slimmed down from the Φ20 of previous models to Φ17, the increase in strength means increased precision.
We eventually reached a level that would enable the qualities of the end tip to be fully utilized.

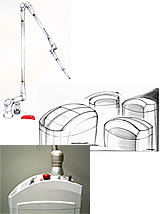
The draft design delivered by the design team was for a new and exciting product.
But would we be able to make it a reality? The task before us seemed impossible.
The plans emphasized natural curves and lines, with a sleek, integrated design right up to the handpiece. However we looked at it, the three dimensional images on paper appeared impossible to render in physical form.
One initial suggestion was that we might make the hinge blocks using die casts, but after several problems were noted with this method, such as peeling paint and scratches, and the issue with color alumite treatments offering low precision even at non-color manufacturing processes, we decided to make the blocks using mechanized techniques.
However, to maintain the design integrity, the aluminum parts underwent alumite treatment, and the pipes, which were the only part made from a different material, were painted to resemble alumite. We worked hard to reach our design objectives, reviewing structure and form issues on a day-to-day basis, and holding meetings with our Ibaragi plant on manufacturing issues, a process that overall took longer than three months.
The color alumite treatment also involved time considerations affected by the amount of pigment used in the dye, the required immersion time and the size of the part to undergo the treatment, all of which contributed to a range of different treatment times. Through the cooperation of the Production Technology Department, the different parts were each produced to a specific timeline, which enabled the coloring process to be managed efficiently.
¦Alumite is the creation of an anodized layer on the surface of aluminum
(the layer is created by the application of a current to diluted sulfuric acid).
Micro-holes on the surface allow pigment dye to seep through, coloring the material.

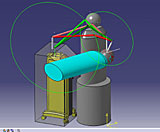
We assessed the angles of the manipulator under different treatment positions, and came across some positions from which it was unable to reach the oral cavity.
We were torn between wanting good reach for the manipulator while also wanting to achieve a compact design.
Using 3D CAD software and prototypes, we realized that it was important to get a balance between long and short pipes. We also realized that we could reach our objective of an apparatus body that was small enough to allow the dentist to have it as his or her side.
Next we looked at getting a balance in the spring mechanism. By losing a lot of weight, we were able to achieve a slimmed down shape but we were also able to achieve a much lower overall weight. This was an essential element in our aim to design a stylish manipulator.
We considered a variety of ideas for spring shapes and mechanisms. We wanted the manipulator to be responsive and flexible when raised, and resistant and sturdy when in a resting position. We also wanted to distribute the weight evenly over a wide area, and ensure strong resistibility. While we could reach those goals by focusing on quantitative calculations, the prototypes all had a rasping sound in the springs...
We were finally able to achieve our goal by optimizing the spring shape, the conceptual approach to the clearance gap, and materials used in for manufacturing.

The opinion of senior management that it would be good to have the Manipulator on a Lite frame was based on the view that the contents were generally the same, and the results would be a product that was still strong but which was also light, which sounded easy on paper but which presented various issues to the development team.
Whatever method we chose, senior management wanted a manipulator that was as light as the fiber-type models. We checked manipulators manufactured by other companies and found that 30kg was heavy, so we aimed for 25kg. That would mean a 40% reduction in the 42kg 03SIISP. But the frames for the OPELASER Lite didn't have the strength to hold the manipulator alone.
Previous models had frames that supported oscillators or optical devices, but we chose a different approach altogether, separating the part touching the optical axis from the frame, and devising a structure whereby the weight borne by the frame is not conveyed to the optical device. Using this technique we removed the need to make the frame stronger than it needed to be, and achieved our objective of 25kg. The technique also contributes to a steadier optical axis by preventing weight being transmitted to the optical part even if pressure is applied to the manipulator.

One of our main objectives was to make sure the manipulator had a sharp laser concentration.
We were able to reduce the laser point diameter from Φ0.4mm to Φ0.15mm, and at the same energy density output as the 03SIISP achieved a value to the factor of seven. This raised the vaporization values, and enabled sharp incisions at low outputs, also helping to prevent blood loss and minimizing the clotting layer.
Furthermore, defocus irradiation on handpiece release is wider than previous models, improving treatment results in narrow oral cavities, with maximum output levels of 7W. Such specifications allow for a wider range of treatments and improved results.
A sharp energy concentration and high output levels, together with its compact and stylish exterior, make the manipulator type CO2 laser apparatus the best choice for professionals.
The OPELASER PRO was developed through the shared vision and commitment of the development team, the production department and partner companies to make it the best possible laser apparatus, a vision and commitment that we feel sure you will recognize once you've experienced the style and ease-of-use for yourself.
|